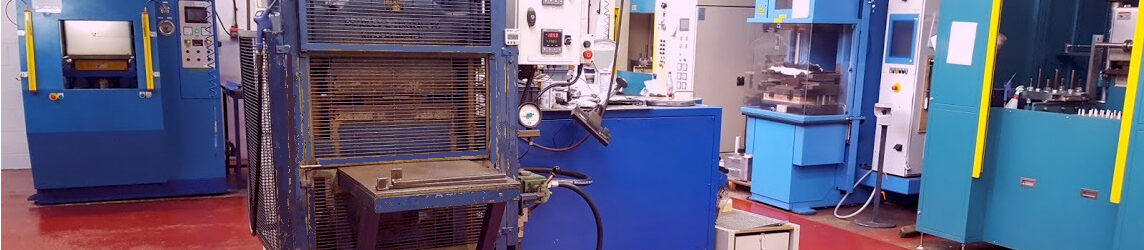
Injection, Compression & Injection Moulding
Butser Rubber are specialist UK based injection, compression and transfer moulding specialists with extensive experience in mass production and prototyping of bespoke rubber components. By investing heavily during the last decade in automated machinery to improve process efficiency and expand as a business to serve a broader range of industries.
Injection Moulding
Rubber injection moulding utilises the viscous properties of rubber at elevated temperatures to form the rubber into a shape defined by a mould. Raw rubber compound is heated to a temperature at which it can be forced through a barrel by a reciprocating screw. The rubber compound is compressed into a mould tool and is then left to cool for a period of time.
Butser Rubber have a number of automated injection moulding machines including a new ‘microshot’ injection machine used for precision rubber components. Our staff are experts in the injection moulding process which enables our products to be excellent quality and consistent throughout manufacturing cycles.
Compression Moulding
In the rubber compression moulding process, heated rubber compound is placed into an open pre-heated mould. The mould is then closed and compressed using hydraulic machinery so that the viscous rubber compound entirely fills the cavity inside the mould tool. As the rubber component cools within the cavity it can be removed and post-processed.
Butser Rubber operate several mid to large compression moulding machines which can be used to manufacture one off components as well as multi-cavity mass production runs. The machinery we use offers excellent process stability and production speeds.
Transfer Moulding
Rubber transfer molding involves inserting heated rubber compound into a pot which is then forced using a hydraulic plunger through a small channel into the mould cavity, comprising of multiple tool parts. As the rubber compound cools down over a period of around 6 minutes. Transfer moulding offers durable and consistent rubber parts.
By utilising our 40 years industry experience, we can provide industry leading custom rubber transfer moulding processes to our customers with provide consistently high quality components that can meet industry standards.